Case Study: Miller Industries (Automotive)
Tennessee and Pennsylvania, USA
Miller Industries Completes Company-wide Conversion to Dialight Industrial LED Lighting
1,750 New Fixtures Across Three Facilities Ensure Outstanding Visibility & Energy Savings with Worry-Free Lighting for Years to Come
Miller Industries is the world’s largest and well-known manufacturers of towing and recovery equipment, building all classes of innovative towing and recovery trucks, car haulers and related equipment. With facilities in Hermitage, PA, in Greeneville and near Chattanooga, TN, plus one in England and in France, its global operations supply the largest dealer/distribution network in the industry.
From a 4-fixture trial to corporate-wide fixture of choice
Just over five years ago, facility managers at the Hermitage plant grew frustrated with the constant maintenance and upkeep required of the antiquated lighting on the shop floor and began investigating options for an upgrade.
What began with a trial of just four Dialight 18,000 lumen Vigilant High Bay fixtures soon transformed into a complete corporate retrofit across all Miller Industries’ facilities. With the completion of the project at Greeneville, Miller’s US facilities are now 100% converted to Dialight’s class-leading Vigilant industrial LED High Bay fixtures and are now fully realizing the benefits of higher quality, more sustainable and maintenance-free lighting.
New process, precision requirements demand better visibility
At its Greeneville facility, Miller was embarking on a new business model: vertical integration of its supply chain. Previously, the company had focused on welding, assembly and painting of prefabricated components, installing outsourced wrecker and rollback equipment onto its truck chassis frames. Aiming to bring fabrication in-house, the company converted 60,000 square feet of its manufacturing facility to a fab shop, complete with high-tech equipment including laser lathes, press breaks, CNC and other modern machining tools.
Because of the precision work required, Bill Couch, general manager of the Greeneville facility, says new lighting was a must.
“These quality tolerances are much tighter than welding tolerances,” he explained. “We have to make sure the staff can read the micrometer accurately and see the finishes clearly. If you can’t see the part, you can’t make a quality part. Not only do we have a reputation to uphold, but this is our first time doing this kind of work, so it absolutely has to meet our standards and be successful.”
Not only was the current lighting inadequate, but dust and dirt accumulation on the fixtures was also a major problem. The old HID high bays were prone to collecting dust, resulting in a yellow-hued light, and they required constant cleaning, which Couch admits, “we weren’t diligent about,” because of the hassle and difficulty involved.
The lights were hard to access and cleaning required blowing the dust off with an air compressor, which of course caused it to rain down on everything below.
“It created a horrendous amount of dust all over the floor, toolboxes and equipment, so then we’d have to clean that up, too. We certainly don’t want our new trucks covered in that,” he said, explaining that the only time cleaning took place was during production shutdowns for inventory. “Which meant it didn’t happen very often, so most of the time we just dealt with poor lighting.”
In some cases, that meant as little as 10-11 footcandles with the current fixtures, with even the 18,000 lumen fixtures in the warehouse only delivering about 63 footcandles.
Dialight: the clear choice
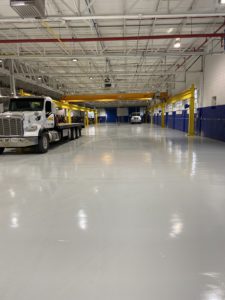
With quality control, facility aesthetics and worker safety on the line, the Greeneville facility embarked on its own lighting upgrade spurred by the success of the Dialight retrofit at Hermitage and Chattanooga.
“There really wasn’t much of a question about whether to use the Dialight fixtures,” Couch says. “The 10-year warranty is the number one reason, along with the ease of installation and their track record for quality and service. We probably quoted three or four different manufacturers; Dialight was competitive on price, and the warranty and ease of replacement sealed the deal.”
In fact, installation at the Greeneville facility went extremely fast. The staff were able to do all the prep work on the ground, cutting and threading the conduit, installing the twist lock and trimming the fixture cord. Once prepped, the conduit was installed and the new High Bay fixtures were hung directly on the conduit, with minimal time spent working at high elevation.
Couch estimates that each fixture took only about 15 minutes each and one electrician was able to swap out a 50×50-foot bay in about 40 minutes.
Undeniable energy and time savings
With the project now complete, the company has realized an average of 15% energy savings per year after installing LED lighting. In addition, Couch estimates his maintenance team now has 60 more hours per year to devote to production-related work—time that was previously spent cleaning of fixtures and bulb and transformer replacement.
In addition, Couch says the improvement in visibility at the Greeneville facility has been an outstanding benefit for employees.
“We gauge their response by their lack of response…when complaints go away, you’re doing something right, and we’ve not heard a single complaint in the finished areas about not being able to see,” he said. “Although, we do have a few small areas that still need to be installed, and we’ve heard lots of complaints from folks there since they see such a difference, but of course, we’re working on that.”
Overall, the Miller Industries team is extremely pleased with their investment in Dialight’s industrial-grade high bay LED lighting technology.
“From the first four trial lights in Hermitage to the completion of the Greeneville facility, the entire experience has been smooth and seamless, from working with the sales staff and technical team on choosing the right fixtures and the best way to install them using our existing hangers, to the quality of the lights and the massive improvement in visibility,” said Jamison Linden, Miller’s vice president of operations. “We’re already halfway through our 10-year warranty at the Pennsylvania plant, and we’ve had zero issues.”
To learn more about Dialight’s class-leading industrial LED high bay lighting solutions, visit dialightdev.wpenginepowered.com.
Installation Snapshot:
- Miller Industries, global towing and recovery equipment manufacturer
- Retrofit across 3 U.S. facilities
- 1,750 Vigilant High Bays installed, a mix of 18K and 19K lumen products
- Estimated energy savings: 15% per year
- Estimated maintenance time savings: 60 hours per year